Le maintien de la navigabilité des aéronefs civils et militaires repose à la fois sur des capacités de réparation des pièces endommagées mais également sur la garantie d’une fourniture rapide pour des composants de rechange, et ce pendant toute la durée de vie d’un programme. A cet égard, la flexibilité offerte par les technologies de fabrication additive permet de soutenir les besoins du marché de la MRO (Maintenance, Repair and Operations) mais également de produire des composants neufs (rechange) à partir des mêmes équipements industriels. Au passage, la fabrication additive peut également opérer comme un puissant bras de levier lorsqu’il s’agit de relocaliser une production sur un territoire, de réduire les délais de fourniture ou pour s’affranchir en partie des contraintes relatives à l’approvisionnement des matériaux.
Dans un contexte de production sidérurgique mondiale tendue, la multiplicité des programmes aéronautiques et des nuances métalliques référencées au catalogue des OEMs impose aux fournisseurs de disposer de capacités de stockage coûteuses et de chaines d’approvisionnement logistique complexes pour sécuriser la fourniture de produits plats (tôles, feuilles, etc.) ou de produits longs (barres, profilés, etc.) nécessaires à la fabrication de composants neufs. Dès lors, certains approvisionnements peuvent s’avérer délicats, surtout lorsqu’il s’agit de nuances anciennes ou de matériaux stratégiques qui font rapidement l’objet d’enjeux de souveraineté.
Dans le cadre du projet de recherche MAMA, l’IRT Saint Exupéry (Toulouse, 31) et la société RECAERO (Pamiers, 09) ont étudié ces enjeux à travers la fabrication d’une ferrure de rechange destinée au super-transporteur Beluga d’Airbus (A300-600ST).
Cette pièce complexe soumise à des sollicitations de type fatigue mécanique est traditionnellement usinée dans une barre de 82kg d’acier inoxydable à durcissement structural X6CrNiCu15-5 (15-5PH). Les cycles longs d’approvisionnement de ces produits associés à un volume minimal de commande et une capacité de stockage importante conduisent à des immobilisations financières pénalisantes pour la compétitivité de l’entreprise.
L’approche alternative mise en œuvre repose sur la fabrication additive en 5 axes d’une ébauche de type near-net-shape avec le procédé LMD-poudre sur une machine de l’IRT Saint Exupéry. Ainsi, la disponibilité immédiate de poudre d’acier en 15-5PH est aisément assurée par une dizaine de fournisseurs. Dès lors, l’avantage majeur d’une matière première sous forme pulvérulente réside dans une rationalisation drastique des stocks, aussi bien en termes de volume que de références. En effet, la poudre permet indistinctement d’opérer une réparation, un ajout de fonction ou la fourniture d’ébauches destinées à être usinées, quelles que soient leurs dimensions. Mieux, l’aval des clients (avionneurs, compagnies aériennes) et des autorités aéronautiques permettrait à l’avenir de simplifier le catalogue de matériaux en remplaçant des nuances obsolètes et parfois indisponibles par des références universelles plus performantes.
Au-delà de la sécurisation de l’approvisionnement en matière première, la fabrication additive permet dans l’exemple étudié de disposer d’une ébauche congrue de 14kg en seulement 10 heures de production et de limiter ainsi la quantité de matière totale engagée. Cette approche frugale répond de manière éloquente aux impératifs actuels de décarbonation du secteur aéronautique car le ratio buy-to-fly initial de 13,7 est réduit à 2,4. Enfin, la phase d’usinage sur machine 5 axes est écourtée de 40% ce qui permet de réaliser des économies substantiels d’énergie ainsi que sur les outils coupants.
En définitive, la flexibilité offerte par la fabrication additive permet de s’affranchir du stockage de volumes importants de matière première pour le remplacement de composants défaillants, ce qui résulte à terme dans l’amélioration du taux de disponibilité opérationnelle des aéronefs civils ou militaires. En sécurisant la chaine d’approvisionnement, la fabrication additive renforce l’offre et la compétitivité des entreprises du secteur tout en répondant efficacement aux enjeux relatifs à leur responsabilité sociétale et environnementale.
A PROPOS DU PROJET MAMA
« Les objectifs industriels résident dans la réduction significative des coûts récurrents de fabrication, des volumes de matière première engagée et le développement de solutions de réparations de pièces aéronautiques à très forte valeur ajoutée. Le projet contribue aussi à une diminution significative de l’empreinte environnementale de l’industrie de la construction aéronautique. »
Débuté en 2018, le projet MAMA, porté par l’IRT Saint Exupéry, a pour objectif la réduction des coûts de fabrication de pièces primaires d’aérostructure et le renforcement de la compétitivité économique de l’industrie française dans le domaine de la construction aéronautique.
En avril 2022, un premier démonstrateur en alliage de titane TA6V de 800 mm de long correspondant à un tronçon échelle 1 d’un cadre de fuselage de l’Airbus A350 avait été dévoilé. Il a permis de démontrer une réduction de matière première engagée en matriçage de plus de 30% par rapport à la solution industrielle actuelle.
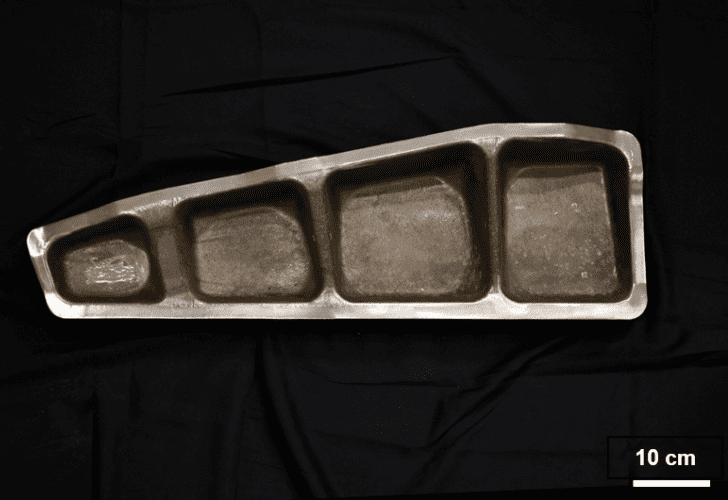
Téléchargez de dossier de presse – Avril 2022
KEY INFORMATION
Chiffres Clefs
Durée du projet : 5 ans (août 2018 – juillet 2023)
Budget : 10.4M € (financés partiellement par le PIA et la Région Occitanie)
Membres : 11
Membres Industriels
Airbus, Aubert & Duval, IRT Saint Exupéry, Mecaprec, OPT’ALM, Recaero, Sciaky