In the face of current environmental challenges, innovation in composite materials is becoming essential in order to find solutions that will eventually enable the use of parts manufactured using processes that limit the use of chemical agents that are harmful to the environment, and to develop optimised circuits for the reuse or recycling of aeronautical parts at the end of their life. The IRT Saint Exupéry is positioning itself in this field with the development of advanced polymer foams. These new foams, which are both bio-based and recyclable, promise optimised performance for a variety of applications. Find out more about the advances and promising prospects of the MOLY project.
The IRT Saint Exupéry’s “Advanced Manufacturing Technologies” division, and more specifically its “Polymers & Composites” skills centre, is working on the development of foams that meet the objectives of designing high added-value parts and the circular economy of composites.
It is within this framework that our teams are working on the development of polymer foams representing new solutions for sustainable composites. To achieve this, they are tackling 5 main challenges: diversification according to applications, the use of bio-sourced materials, the use of recyclable or reusable materials, the introduction of processes that limit the use of chemical agents, and the integration of the concept of multidisciplinary modelling to optimise and predict the behaviour of processes and structures.
The EF-MOLY feasibility study: promising results
Classified as thermoplastic materials, these foams are recyclable, made from bio-based materials and manufactured without chemical foaming agents. In addition to their composition, these materials offer optimised properties for thermal, acoustic and vibro-acoustic applications.
An initial feasibility study, called EF-MOLY, focused on foaming thermoplastic and biosourced polymers with controlled porosity. In collaboration with our partners (Airbus, Institut Clément Ader, ISAE SUPAERO, Centre Rapsodée – École des Mines d’Albi RAPSODEE, STAE), this study looked for alternatives to NOMEX fibre foams (non-bio-sourced, non-recyclable) and aluminium honeycombs (no thermal, acoustic or electrical insulation).
Our team therefore manufactured a biosourced thermoplastic foam with different levels of porosity that can offer acoustic, vibro-acoustic, thermal and dielectric insulation properties. To achieve this, a new continuous CO2 manufacturing process was developed.
The study also identified technological and technical obstacles to optimising porosity for characterisation and industrialisation.
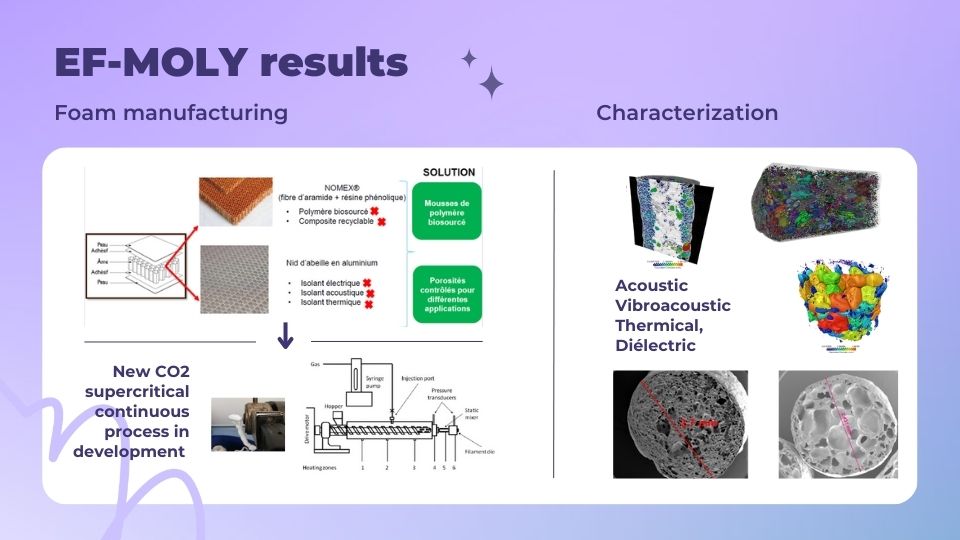
Let’s go further with the MOLY project
On the strength of these promising results, the IRT Saint Exupéry team and its partners want to go even further by optimising the performance of polymer foam parts manufactured using eco-responsible processes. MOLY is a project that offers a solution that ticks all the boxes for tomorrow’s main challenges and can be applied in all areas of activity: construction, wind power, naval and aeronautical engineering. The polymer foams developed will have to meet expectations in terms of high-temperature resistance and high-performance characteristics, while also being biodegradable. The aim is to achieve acoustic, vibro-acoustic, thermal and dielectric insulation properties while optimising mechanical properties and impact resistance.
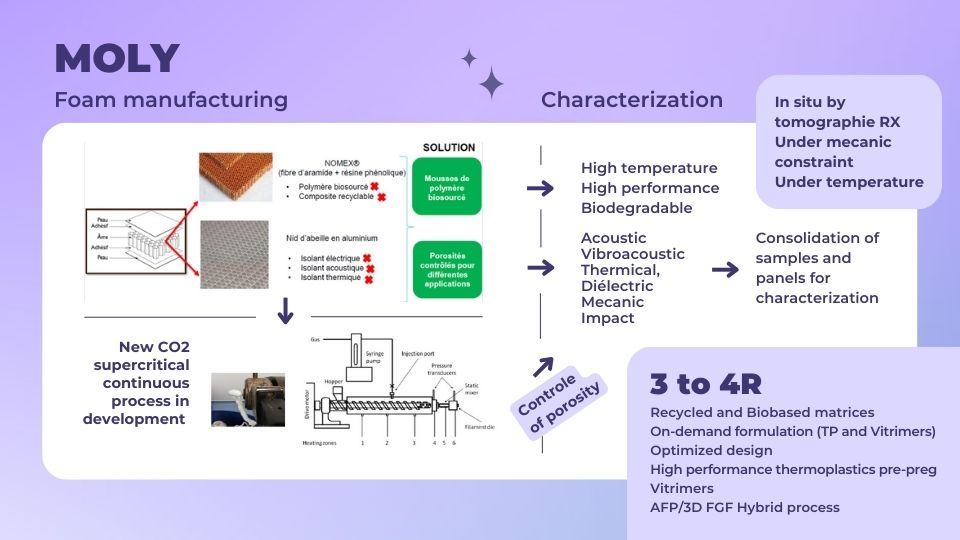
Project objectives:
- To develop high-performance polymer foam materials that are resistant to high temperatures and morphologically controlled.
- To model physical phenomena in order to optimise the design in terms of acoustic, vibro-acoustic, thermal, dielectric and mechanical performance by controlling the morphology of the foam.
- Setting up a platform for producing large-scale architectural foamed materials.
To achieve this, the project members will be able to build on the initial results of the CO2 process already developed and optimise it for industrialisation. Porosity will be controlled using IRT Saint Exupéry’s equipment and skills, including the use of optimised, non-destructive characterisation (X-ray tomography) and numerical tools for modelling behaviour and limiting experimental designs.
Applications and members
A large number of members, representing various sectors of activity, are already involved in the project. The applications for this new polymer foam are many and varied. Our members include players from the aeronautical, naval and space industries, as well as textile and sports equipment manufacturers. This diversity bears witness to the vast and innovative potential of this innovation.
Call for new members
Are you a laboratory, start-up, SME or large group interested in joining us? Your expertise and innovative ideas will be invaluable in driving the MOLY project forward! Be at the heart of sustainable innovation and become a key player in this adventure! Contact: caroline.lyszyk@irt-saintexupery.com